Requirements
In recent years, the process of PCB assembly has fundamentally changed. Conventional Through Hole Mounting Technology (THT) is increasingly being replaced by Surface Mount Technology. However, in many areas of the electronics industry, there is still a need for THT technology. For certain components, there are increased mechanical stresses. Relays, coils, capacitors and connectors are soldered with modern selective soldering or the established wave soldering processes. The first-pass yield of selective or wave soldering is typically much lower than for the reflow process. Typical errors include open solder joints, solder bridges and solder balls. High quality and reliability standards requires test and inspection tools that not only provide all the information for a repair facility, but also allow an optimization of the process. Even with intensive testing and high mix products, test times must be within the production cycle in order to achieve high productivity.
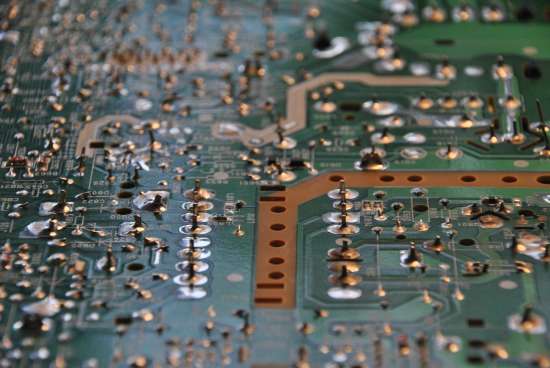
Solution
Automatic inspection using modusAOI ensures rapid and complete examination of all soldered PCBs. The combination of multi-color LED lighting and color line scan camera enables clear meniscus and short circuit inspection. The full-field imaging technique of scanning allows the 100% recognition of scattered solder balls. Compared to manual inspection, test results with modusAOI is not operator dependent, but always objective and reproducible. The inspection allows a rapid feedback of process errors (closed-loop). The test results are displayed at the rework stations, to document the repair of the PCBs. The results give time and cost savings as well as a significant increase in quality.
- modusAOI saves time, space and therefore money.
- typical payback time: eight to twelve months
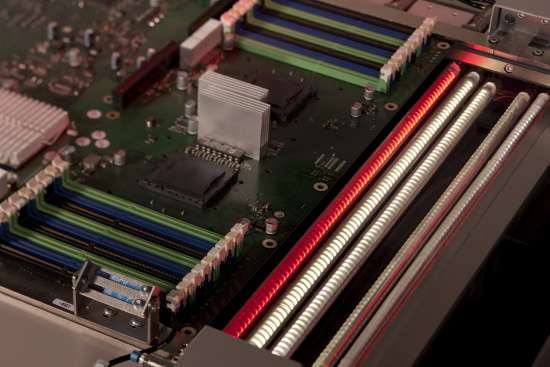
Features
Reliable fault detection
- Solder bridges, solder splashes
- Scattered solder balls (within full surface) up to 100µm
- Open solder joints, missing pins, bent connectors
- Recognition of DMC / barcode on the verification side without additional Reader
High inspection depth and large test range
- High-resolution color scanner
- Multi-color LED lighting
- Real 24-bit color, 14.040x20.400 pixels per scan
- Test range: max. 420mm * 550mm
- High speed: 25mm/sec
- Achromatic lens for parallax free display
Simple user interface
- Indication of fault location and display of error and comparison image
- Identical presentation to the test system and repair stations
- Fault is easily assigned by pressing the statistics button
- Training of operators within minutes
Statistics and process control
- Traceability by evaluating barcode/2D-Code/RFID
- Cost savings due to fast process optimization
- Intuitive test plan creation
- GUI
- Powerful and flexible test algorithms
Under floor system
- Inspection of the PCB bottom side without flip unit
- Seamless integration into the manufacturing process behind the selective and wave soldering system
Double system
- Double-sided inspection of THT solder joints and components inside line cycle time within one unit
Line integration
- Flexible repair station concepts
- Easy integration into the placement line
- Data mapping by barcode/2D-Code/RFID
Offline system
- Easy handling with drawer and variable PCB fixtures

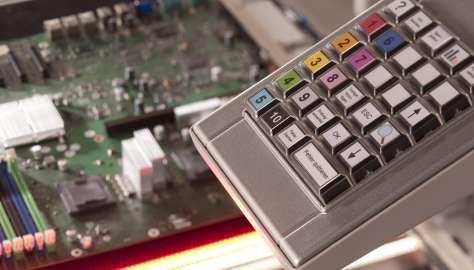
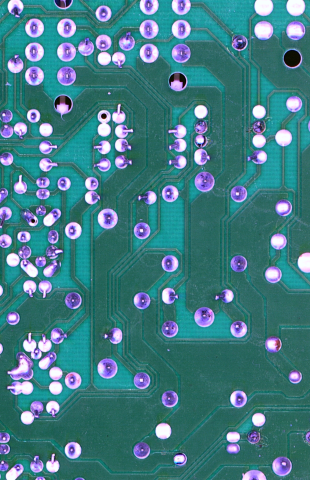